Covid-19 rapid test
A combination of machines providing, labeling and packing
Corona presents challenges to the country. Test cassettes are needed to detect antibodies within few minutes using a blood sample. Strong demand for the cassettes results in fully automated plant manufacture. The Kraus Maschinenbau company specializes in feeding solutions as required. Complex packing machines have been designed by the staff, developed and manufactured on behalf of Senova Immunoassay Systems. Test cassettes and strips are taken over from prior processes and are jointly packed in pouches. In close cooperation with cab, a PX Q print module and an IXOR labeling head integrate for labeling the pouches uniquely in accordance with pharmaceutical regulations.
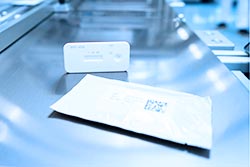
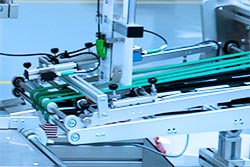
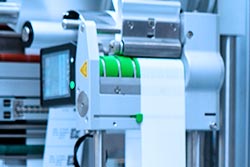
Customized solutions
Joachim Kraus founded his company in 2008. Friction feeders are his subject. In addition to packages no more than 30 mm thick, other flat products such as package inserts, folding box blanks or brochures can be fed or separated. Solutions are put into operation customerspecific wherever, in addition to standard feeding or separation, products must be packed, marked, labeled, tested or counted. cab units have proven effective in Kraus machines designed for applications requiring label printing. In the Senova project, Mr. Kraus decided for cab in labeling as well. Why, he tells in an interview.
Which factors have been decisive for choosing cab?
Kraus: In the end, human beings make the difference. There has been a close relation to Michael Kuerner for many years. He has not only been selling us devices, but also provides technical competence on a high level. If anything does not work a 100 percent, and this might happen in project business, he takes a wrench in his own hands to find a solution. We very much appreciate this pragmatism.
What about the technical aspects?
Kraus: In practice, we soon got aware of the high quality of the cab units. They provide a rugged construction and all the interfaces necessary to realize projects even related to Industry 4.0. In plants, they operate autonomous, interact among each another, with host computers or the plant control unit by cable or WLAN. MQTT assures communication, the industrial standards Modbus, OPC UA and Ether-Net/IP as demanded from many customers are supported. To integrate the units in our machines mechanically, cab provides accessories and the required aids for assembly.
In a series of machines dedicated to antibody tests we will now deliver already the second one to Senova. As regards the initial one, cab evaluated all our requirements very quickly and transferred them to the specifications of the printers and labeling units. As a result, we got exactly the product we required. In cases Mr. Kuerner or any other cab specialist are not available in person at short notice, cab’s technical hotline supports. We have made positive experiences on this as well.
- Running the second machine of a series: Joachim Kraus (pictured left) and Michael Kuerner, cab consultant for systems dispensing printed labels
- Each label of a pouch receives a code containing data specific to the product.
An overall concept, as it is now being implemented, had not been on target initially.
Kraus: That‘s right. Senova initially asked for an individual solution to feed plastic pouches. In a project meeting, we jointly analysed the subject. We agreed that an overall concept consisting of several processes and machine components makes sense. Considering the current state of Corona worldwide, you can certainly imagine that time was short for putting all this in operation. Our constructors and parts manufacturers operated under high pressure in shifts. The machines are assembled, initially operated and accepted by the customer inhouse prior to delivery. Quick decision paths between the construction, purchasing and assembly departments enable us to deliver at short notice if required. This was also a clear advantage here.
Tell us about the operating principle of the machine.
Kraus: In prior processes, the raw materials of test strips are separated and the strips inserted to cassettes. A friction feeder separates ready-made plastic pouches. The test cassettes and the prepared pouches are transferred to the packing machine. The PX Q prints product-specific data on labels. The printed labels are transferred to IXOR to be applied on the pouches. At this, the pouches remain in motion on the conveyor belt. The labeled pouches are kept open by vacuum, test cassettes including strips are inserted, the filled pouches thermally sealed and finally collected. Product transfer from one process to the next is controlled by PLC, so are all the processing steps.
- IXOR is labeling at full speed.
- On its peel-off plate a sensor is detecting each label.
How important is the labeling?
Kraus: Subsequent to the blood sample, the antibody test provides information on whether there is a Covid-19 infection, the person tested is immune or has not yet come in contact with the virus. The test cassettes are pharmaceutical products. Each cassette must be clearly identified compliant to the regulations on serialization and traceability and packed in accordance with pharmaceutical standards.
- PX Q and IXOR complement perfectly and thus increase productivity in marking.
Printing
PX Q is a module designed by cab for pure continuous printing in industrial environments. Several thousand labels can be printed per day and the printed labels in subsequence provided, for example to be applied by a labeling head, in this case an IXOR. Printed labels are provided to the right or left. The print module is 25 cm wide, 30 cm high and less than 40 cm deep, making it easy to integrate. The print method is thermal transfer. Depending from the field of operation, thermal markings remain legible during processing and storage, resist extreme temperatures, liquids and solvents. Sharp-edge definition and high contrast enables even smallest information be verified on a label.
Labeling
Printed labels are applied by IXOR to products exactly on position. A high-torque servo engine allows conveyor belts running with 200 meters per minute even in continuous operation. Depending from the device configuration, the label material and the size of a label, a maximum of 2,400 labels per minute can be applied synchronous to the speed of the product. The device control is part of the base unit. Its casing only 54 mm deep, IXOR accommodates in small installation space.
Detecting
To detect even smallest height differences of 1/100 mm on material webs in motion, the CEON high-tech sensor must be assembled as close as possible to the peel-off plate on the IXOR. At this spot, the effect of material stretching is low and the detection of labels peeled off guaranteed. As the label web remains tight, each label is stabilized while detected and transferred. CEON proves strong in particular with transparent adhesive labels in no-label look, very thin opaque or metallic materials.
Machines by professionals
Kraus Maschinenbau GmbH stands for feeding and separation solutions. In the city of Spaichingen, Southern Germany, 45 employees design, develop and manufacture components and machines for customer projects worldwide, in particular pharmaceutical, logistics and e-commerce businesses.
Products in use
August 2020